ETA Approved Anchors, Why Everyone Should Be Using Them
Posted on 12-02-2020
Regulations and product approvals are becoming more and more stringent across the industry and anchor fixings, often used in safety critical applications are certainly no exception. Guidelines state that safety critical applications are those in which a failure could result in a collapse or partial collapse of a structure, cause risk to human life, or lead to significant economic loss. Not something anyone wishes to be involved in! However, an understanding of the relevant guidelines and what ETA approvals are can go an awful long way in ensuring this doesn’t happen to you.
What is Driving the Need for Change?
Over the past decade or so there have been a number of major failures resulting in serious injury and death. To give an example, a section of ceiling ducting collapsed at a school in Kent injuring 12 children. Upon investigation, it was found that an unsuitable anchor had been selected. There are various reasons why a situation such as this could occur, however some of the most common are:
- An incorrect anchor being selected in the first place.
- A specification change further down the line leading to an unsuitable anchor being selected.
- The incorrect anchor being ordered by an installer due to the original packaging/brief being lost, or the person in charge not being available.
- Incorrect installation.
If an anchor is incorrectly selected or installed, it will likely fail in one of the following ways:
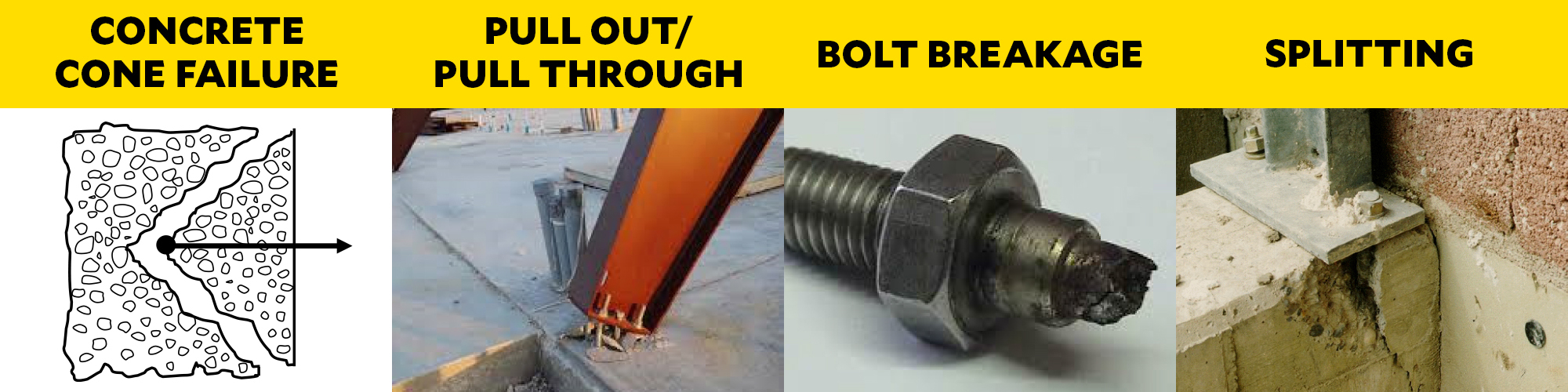
How are Regulations Evolving?
In light of these failures, the Construction Fixings Association (CFA) concluded that the rules and regulations around anchor fixings needed addressing, thus leading to the introduction of BS 8539:2012. BS 8539:2012 is now the standard Code of Practice for anchors used in concrete & masonry and is aimed at everyone involved in the process, from contractors right through to testers. The overriding message from BS 8539:2012 is that ETA approved anchors should be used wherever possible.
What is an ETA?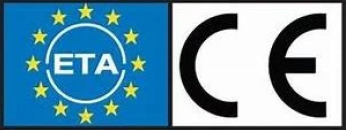
In simple terms, an ETA (European Technical Assessment) is a worldwide recognised framework which contains detailed reports and performance information about the product.
Published in a standardised format, an ETA document will set out what applications the anchor is suitable for, it’s application limits, performance characteristics and how it should be installed. To gain an ETA, a product must have been rigorously tested to strict EU derived standards known as EADs (European Assessment Documents). For further information on EADs (Formerly ETAGs) and ETA testing, see the CFA Guidance Notes.
A product with an ETA will be clearly labelled and will feature an option number. ETA’s are split into 12 options which dictate what parameters they are suitable for, such as for use in cracked or non-cracked concrete. For those specifying anchors, ensuring the chosen anchors’ ETA number correlates with its application is crucial in the safe selection of an anchor. For more information on ETA options, see the table below.
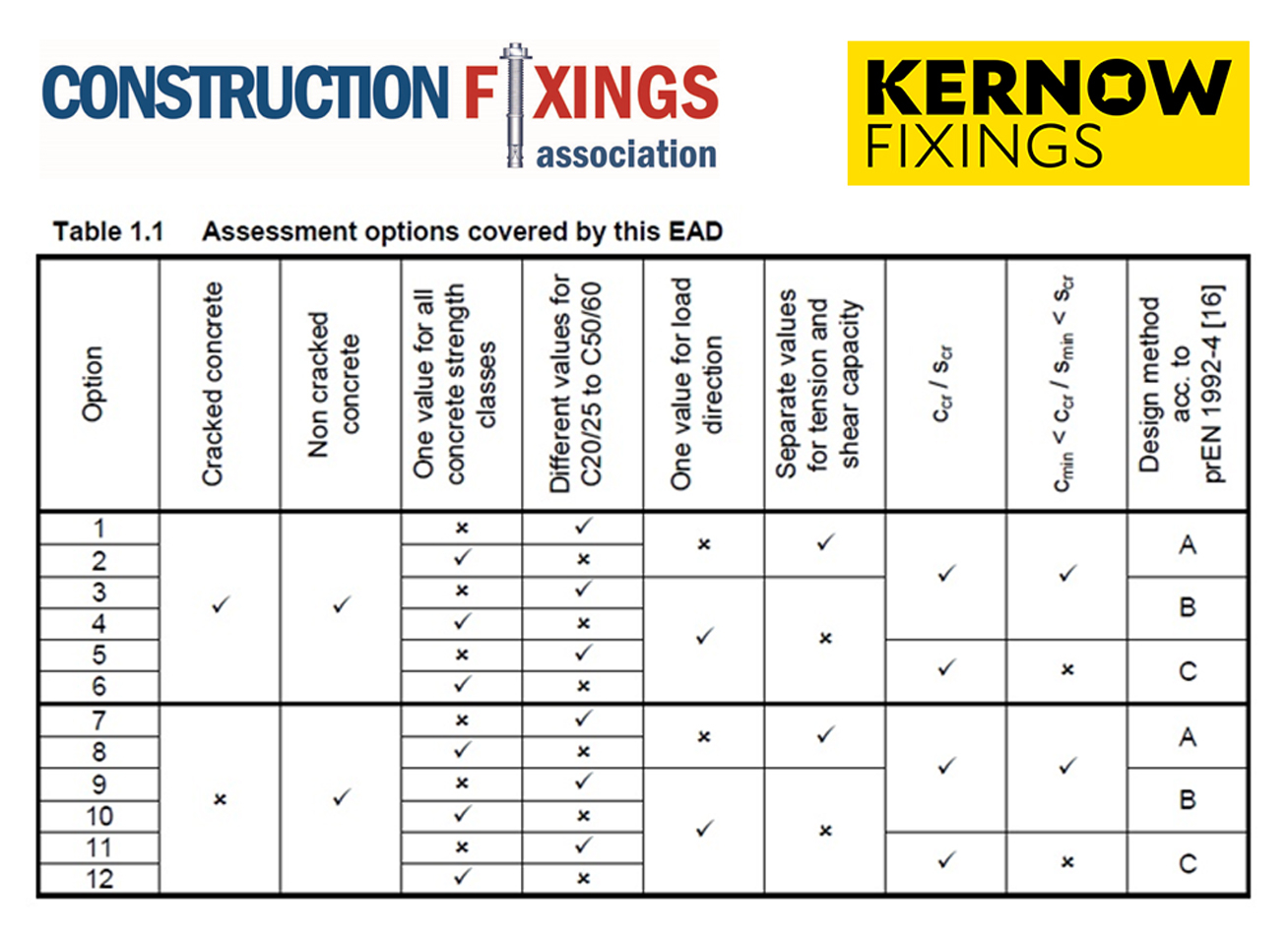
Why use ETA Approved Products?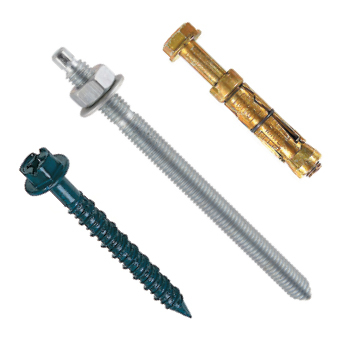
There are many good reasons why ETA approved anchors should be used, but perhaps the main reason is that providing the product has been selected and installed as outlined by the ETA, then there is a guarantee that the anchor will not fail. This not only provides you as a contractor with a certainty that the product is fit for purpose, but also safeguards all who are involved with selecting and installing the anchor.
All the information needed to install an ETA anchor is supplied with the product. From general installation procedures such as torque settings and curing times for resins, to potential issues, such as what to do if the anchor hits rebar. Any competent installer should be easily able to follow the provided instructions, again offering the contractor peace of mind knowing that everything is in place for the installation to be carried out correctly. It is also worth noting that providing the anchor has been chosen and installed according to its ETA document, then the anchor will not need a product test as it has already passed rigorous testing procedures.
ETA approved anchors are also all CE marked which ensures that each anchor is of the same high standard to those which were tested. Not only does this give further assurance to the product, but it also provides a degree of certainty that the anchor will not be sensitive to reasonable variations such as moisture or temperature fluctuations.
There are plenty of other non-ETA anchors on the market, some even being supplied with their own performance data, but how can we be sure that this data is reliable and accurate? How stringent were the tests and how can you as a contractor be sure the testing is relevant to your project? Determining anchor performance is an extremely difficult process with many variables that aren’t easily replicated during testing. The ETA testing procedures are as stringent as it gets with every aspect of anchor performance being evaluated, simply to ensure the results are as reliable, accurate and standardised as possible. Will non-ETA anchors have had such thorough testing with the same guarantees as those with an ETA? No one can say for sure, which poses the question, why would you risk it?
How Can Kernow Help?
We've got the Kernow-How
We know how much of a headache approvals and specifications can be which is why we’re on hand to make your life easier. On a daily basis we work with large manufacturers and supply fixings from those well regarded in the industry such as Walraven, Spit and Fischer, so whatever queries or information you may require, we can get the answers, not to mention being able to supply a whole range of ETA approved fixings.
Specified Fixings Boards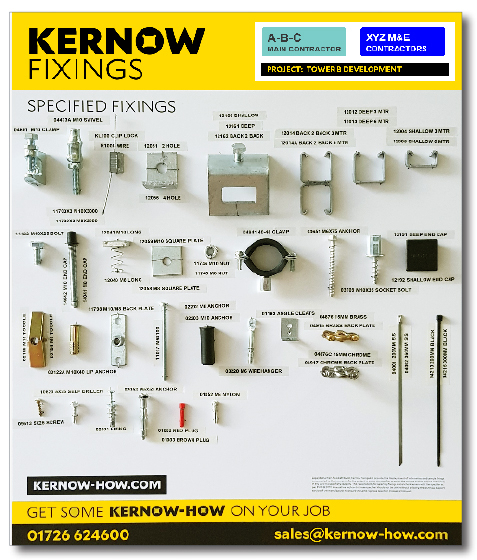
If you are the one responsible for ordering the correct anchors and fixings, how can you be sure that the correct products are obtained on all re-orders throughout the project and not just on the original order? With so many variations of fixings available from a whole host of manufacturers, ensuring the correctly specified product has been supplied every time can be very difficult, often impossible further down the line!
Here at Kernow we have a simple solution in the form of a Fixing Board. These bespoke boards are designed to help our customers by displaying each specified fixing for the project including product codes to re-order. A key communication tool than can be placed on site to:
- Communicate contractor’s specified fixings to all involved on-site
- Avoid orders being placed for incorrect (unspecified) anchors
- Avoid incorrect supply due to clear stock codes being used
- Avoid incorrect fixings being used for the application
- Save time wasting on-site working out which anchor to use
Compliance with regulations and standards is extremely important and something we take very seriously. We have recently worked with some of the largest UK main contractors to incorporate our Fixings Boards into their nationwide Fixings Strategies. Let us help you too.
- Unsure what fixings to use?
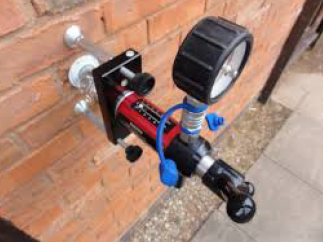
- Need to have pull-out tests completed?
We can take care of this for you, co-ordinating with the relevant fixing manufacturers and arranging on-site pull-out tests as required, supplying a Fixing Board displaying the specified and tested fixings, for easy re-ordering, together with pull-test certificates, any data-sheets required and full ETA documentation.
Summary
The overriding message endorsed by the CFA is that ETA approved anchors should be used wherever possible. ETA approvals provide evidence and certainty that subject to correct selection and installation, the anchor will not fail. With that guarantee, why would you use anything else?
Need more information on anchor selection? Give us a call where one of our friendly team will do their best provide you with the Kernow-How when it comes to anchor fixings!
** Following on from Brexit, CE markings and ETA approvals were set to change for products sold within the UK. It was initially held that CE Markings were to be replaced by a UKCA marking (UK Conformity Assessed); Harmonised Standards (hEN) replaced by UK Designated Standards, ETA's replaced by a UKTA marking, and EAD's replaced by a UK equivalent which has yet to be developed. However, as of September 2024 the UK Government as announced that CE Marks & ETA approvals will remain valid in the UK indefinitely, past the previously proposed deadline of June 2025. This means that both CE & UKCA marks will be valid in the UK, both guaranteeing a quality and fully tested product.